Take a look at our FAQ to support design for galvanising
1. Why must steel fabrications be designed specifically for galvanising?
Steel fabrications must be designed for galvanising to ensure the process is safe and effective. The high temperature of the galvanising bath (around 450°C) requires specific design considerations, and materials like aluminium and stainless steel cannot be galvanised.
2. What are the key design considerations for venting and drainage during galvanising?
- Proper venting and drainage are essential to allow zinc to flow freely and avoid explosion hazards from trapped air or vaporised liquids.
- Sealed compartments in fabrications must be vented to prevent explosions.
- Cropped corners in square-shaped fabrications ensure an even flow of zinc and a smoother finish.
- Hollow sections must have holes connecting the sections or be individually vented for complete zinc protection.
3. What are the minimum requirements for drain holes?
- No drain hole should be less than 10 mm.
- Preferred minimum drain hole size is 25 mm.
- Large hollow sections require a 100 mm diameter drain hole for each cubic metre of enclosed volume.
- For hollow sections like tubes, RHS, and SHS, the drain hole area should be at least 25% of the section’s diagonal cross-section. Leaving the ends of these sections open is preferred.
4. Why is surface contamination a concern for galvanising?
Clean steel surfaces are essential for good galvanising. Contaminants like silicone, suds-type oils, or anti-spatter sprays can cause bare spots or defects after galvanising, potentially requiring costly re-galvanisation.
5. How can surface contamination issues be avoided?
To avoid surface contamination:
- Ensure steel is thoroughly cleaned before galvanising.
- Avoid using silicone-based products or oils during fabrication.
- Inspect for contamination, as it may only become apparent after galvanising.
6. What precautions are necessary for contacting surfaces?
- Large, flat contacting surfaces should be avoided where possible.
- If unavoidable, edges of contacting areas must be continuously welded.
- Holes should be drilled through both members to prevent explosion hazards in the galvanising bath.
7. Why are explosion hazards a risk during galvanising?
Sealed compartments or unvented sections can trap air, moisture, or liquids, which can vaporise at high temperatures, causing dangerous explosions when dipped in molten zinc. Proper venting and drainage eliminate this risk, think about this during design.
8. What happens if design rules for galvanising are not followed?
Failure to follow design rules can lead to:
- Poor-quality galvanising with uneven coating or bare spots.
- Safety hazards such as explosions in the galvanising bath.
- Increased costs due to the need for rework or repairs
Want to ask another question – get in touch HERE
Or download our FAQ to help with your design for galvanising at Forfar Galvanisers Limited
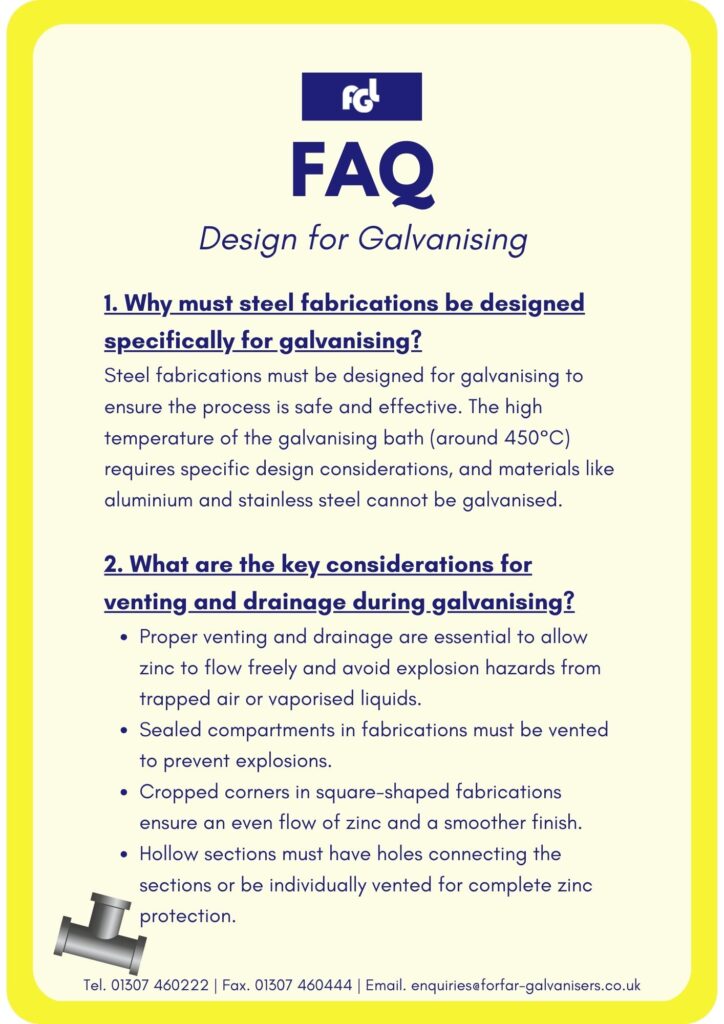
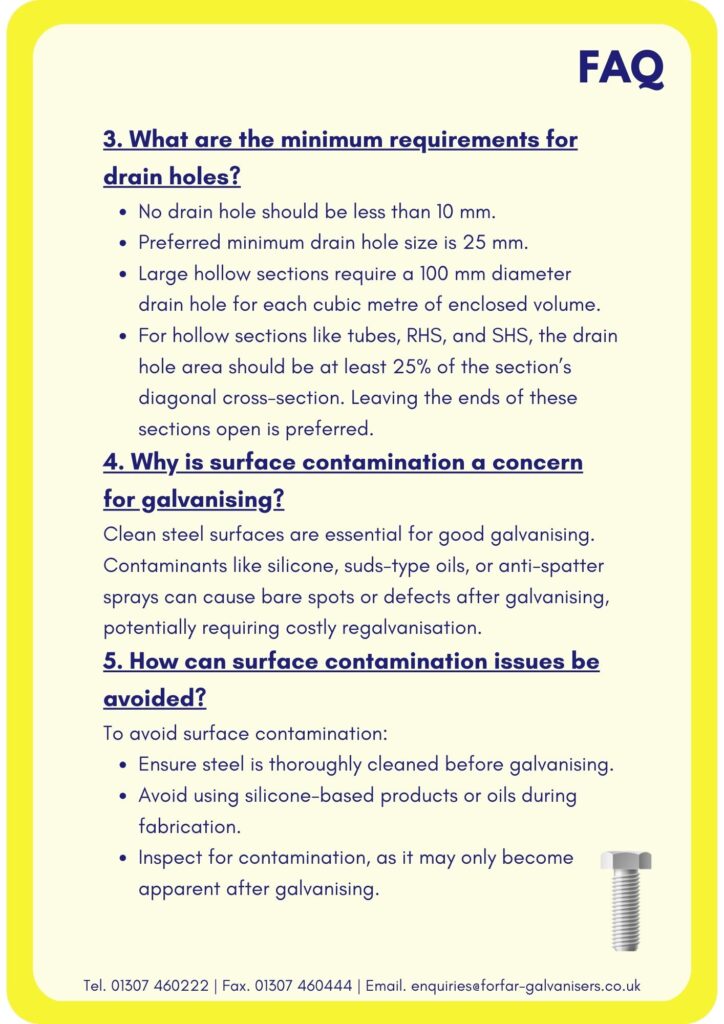
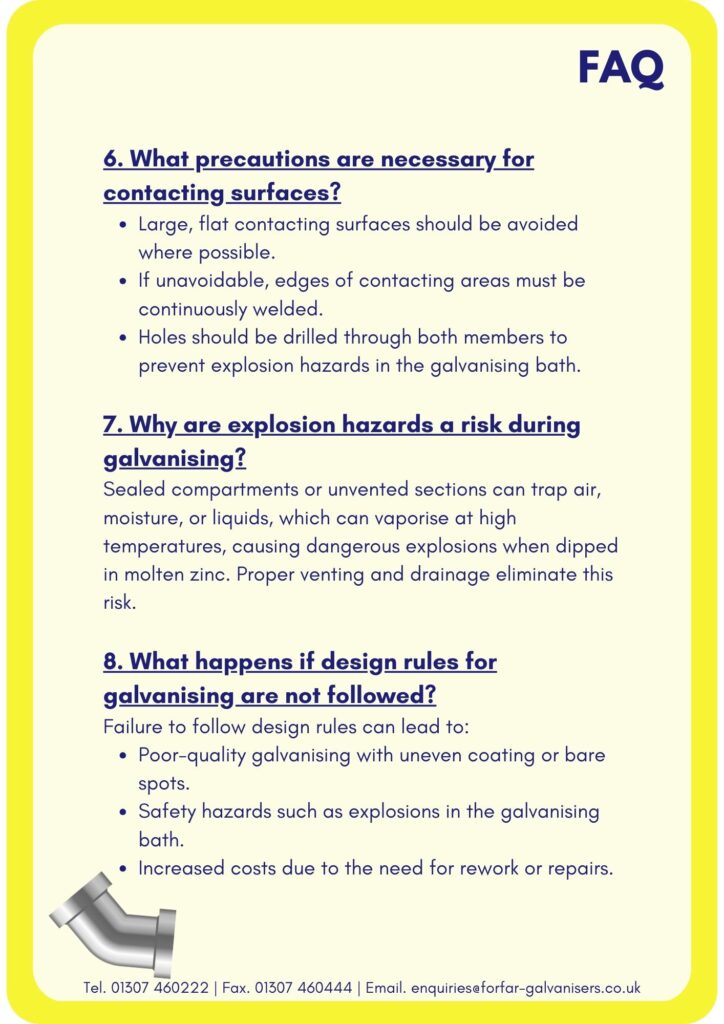
Recent Comments